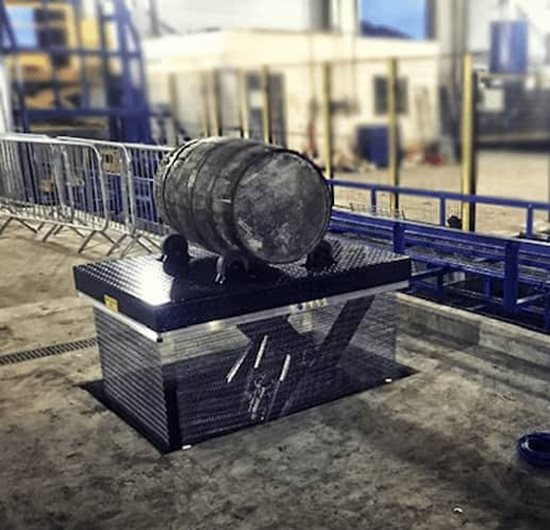
ATEX Solution Improves Working Conditions At Major Whisky Producer
Better ergonomics and safer manual handling
A traditional whisky cask filling operation in Scotland needed to improve the manual handling and ergonomic working position for its workers. The process involves the filling of various sizes of wooden casks with spirit which are then automatically handled on a chain conveyor system for loading and placing in bond to mature.
Cambus TCFS is a high-capacity whisky producer operating around the clock to fill, seal, and mature wooden casks of various sizes.